マーク背景透過.png)
自動車部品の生産から工場の運営サポートなど、さまざまな事業を展開することで国内の自動車産業を支えてきた協豊製作所。
生産に入る前の生産準備フェーズを管理するために長年生産準備システムを利用してきたが、2020年JSOLの組立製造業向けPLMソリューション「ものづくリンク」へと刷新した。
課題
● 取引先のニーズの変化や時代の変化に対応できる生産準備システムに変えたい
● データが部署ごとに異なる方式、別のサーバーで管理されており、データを集約して一元管理したい
● 日程管理が限られたメンバーだけで行われており、確認のために問い合わせる必要があった
解決
● JSOLの組立製造業向けPLMソリューション「ものづくリンク」の導入
効果
● 生産準備に必要な情報をものづくリンクに集約。担当者間の問い合わせが激減
● 原価は部品評価に基づき自動算出。原価管理の業務も負担軽減、期間も大幅短縮
● 車型日程表、生準日程表などを全員で共有し、今やるべき作業が明確に
● どの部署で何の情報をどのタイミングで入力するかを明確にして業務改革も実行
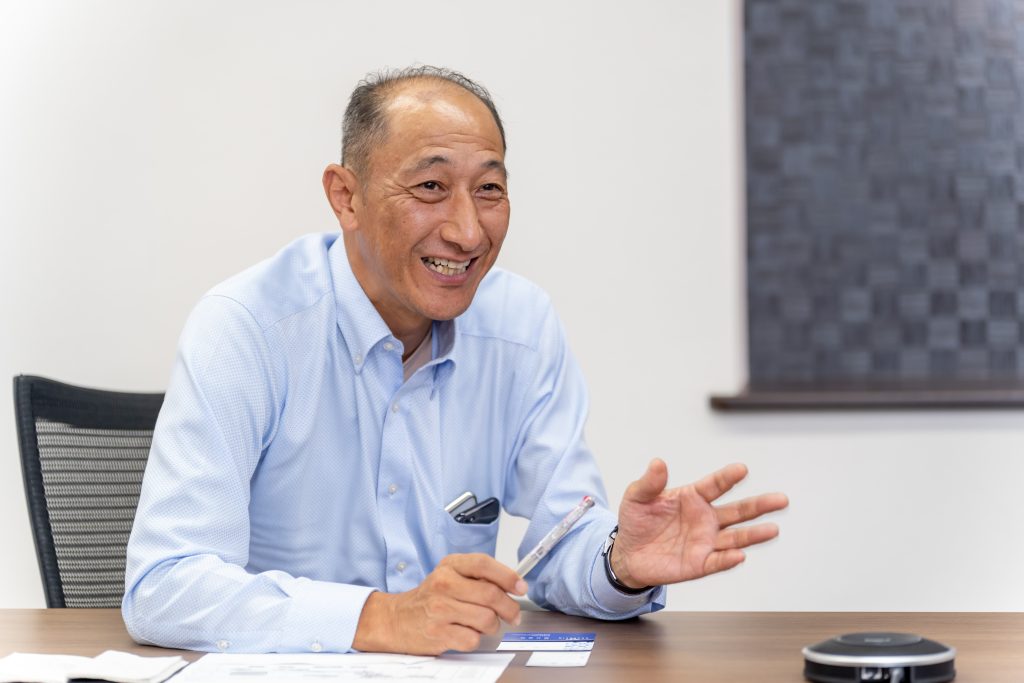
執行役員
システム開発統括
小島 芳紀 氏
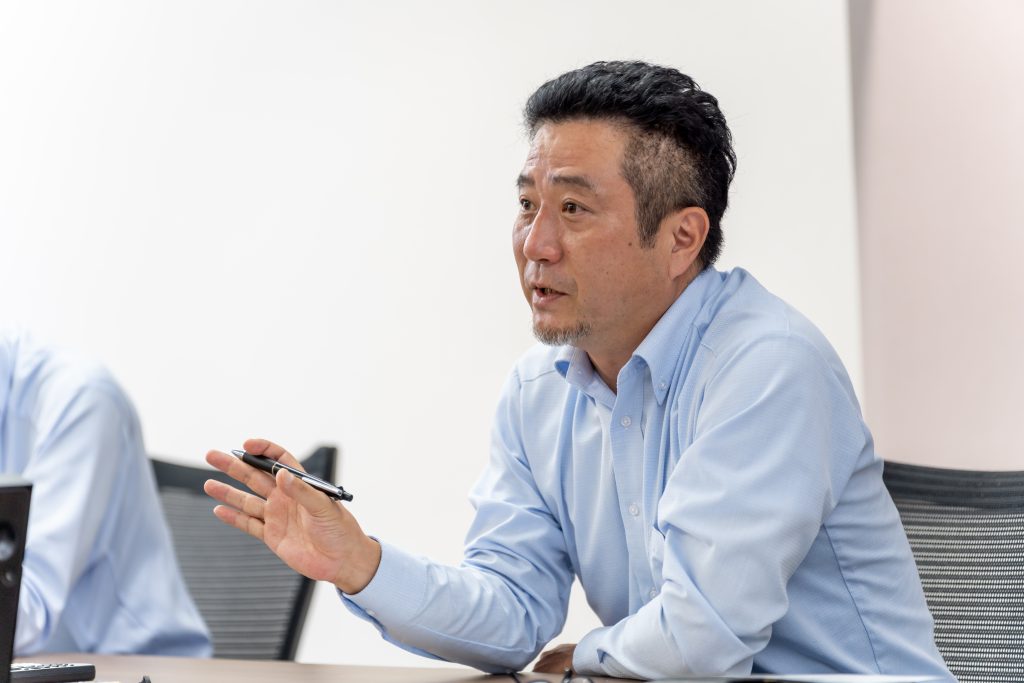
生産管理部 生準管理室
進行管理G
室長
日下 晃 氏

BR生準改革室
主幹
深見 文春 氏
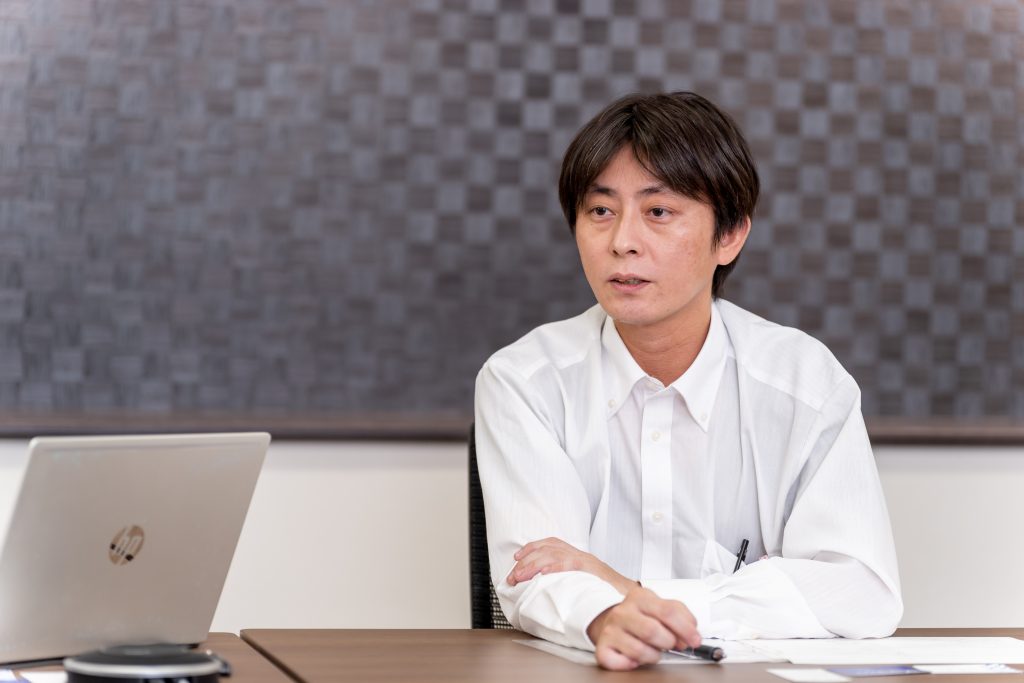
BR生準改革室
担当員
島谷 一慶 氏
技術革新に対応できる柔軟さを持った生産準備システムが必要
自動車に用いられるボデー部品を中心に、電気自動車のバッテリーやモーターなどのユニット部品、製造に用いられる機械やETCレーンなどの設備、工場の安全や保全を支援するファクトリーなど、さまざまな事業を展開してきた協豊製作所。
執行役員の小島芳紀氏は、自社の特徴について「トヨタ自動車の100%子会社であり、地理的にも近く、課題を共有したり相談しやすい関係性を強みとしています。ボデー、ユニット、設備、ファクトリーという4つの柱を組み合わせた新たな事業にも取り組みたい」と説明する。
そのようなものづくりにおいて、「生産管理システム」とともに重要なのが「生産準備システム」である。取引先からの受注情報を共有し、企画、設計、試作などを行う生産準備のフェーズでは、営業や技術、調達など多くの部門が関わる。その過程では仕様変更、日程調整なども頻繁に発生し、関係部署で共有しながら生産に向けたプロセスを踏んでいく。
以前利用していた生産準備 システムは、2007年に導入した市販パッケージだった。小島氏は「昨今、情報のやり取りの方法や必要とする情報が変わってきたこともあり、以前の生産準備システムは部品表の展開だけに使われているような状況でした。また日程短縮、多品種の連鎖立ち上げなど、取引先からのニーズも高くなっており、対応していくにはシステムを変える必要がありました」と当時の課題を説明
する。
生産準備を担当している生産管理部 生準管理室 進行管理G 室長の日下晃氏は、システム刷新の目的として「情報を一元化し、信頼性向上を図りたかった」と述べる。当時も部品表は生産準備システムで管理されていたものの、各部署が自分たちで使いやすいよう加工して活用していたため、実際に使われているデータが部署ごとに違っていたり、ファイルを保管するサーバーが違っていたりしたのである。
同じグループ会社で重用されていたPLMソリューションを検討
システム刷新を検討していた時期、ある講演で同じトヨタグループの豊田鉃工が新たな生産準備システムを導入したことを耳にした。その講演で「ぜひお薦めしたいシステム」と紹介されていたのが JSOLの「ものづくリンク」だった。その後、JSOLからものづくリンクの提案を受けたときの印象を、BR生準改革室 主幹の深見文春氏は「本当にドンピシャと感じた」と振り返る。
「新たなシステムで実現したいポイントに、(1)情報の一元管理、(2)登録情報の精度と鮮度の追求、(3)申請承認決裁作業のシステム化、(4)基幹システムとの連携、(5)日程連動と関所管理、(6)機能別資料の自動作成の6項目を挙げていましたが、それらの要望にすべて対応できると見込めました」(深見氏)
決定の前にはJSOLのメンバーと共に豊田鉃工様の運用状況なども確認した。そのときの印象を、BR生準改革室 担当員の島谷一慶氏は「実際に利用されている画面を見ながら活用ノウハウなどを聞かせてもらい、システム化への道筋や適切な管理のやりかたなど具体的なイメージができました」と語る。
ものづくリンクの導入にあわせて業務の見直しにも取り組んだ。以前は、取引先との窓口となる営業を起点とした仕組みだったため、受注情報や部品表などは営業がシステムに登録していた。ところが、登録された情報をエンジニアの視点で見ると曖昧な要素が含まれていることもあり、後工程のスタッフが再度確認・修正していたという。
そこでものづくリンクの導入時には、「受注情報を営業が入力」して「部品表は技術スタッフが登録」する。「生準管理室で確認」後、「プレス技術・設備生技・調達などの部署にデータ入力を回す」というように、何の情報をどの部門がどのタイミングで入力するかを決めていった。
「約1,500にも達する生産準備プロセスを分析したところ、重複も見つかりました。そこで各部署が行うプロセスを明確にし、ものづくリンクのワークフロー機能に乗せてスマートに流れるようにしたことで、業務改革も実現できました」(深見氏)
STEP1でデータの一元化と原価管理、STEP2で日程管理と2段階で整備
JSOLではプロトタイプを活用してものづくリンクの構築を進めた。利用部署は多岐にわたるため、各部署からキーマンとなるメンバーにプロトタイプを見てもらい、現場の意見を集めて開発に反映させていった。
「紙芝居のように動かない画面で説明を受けるより、実際に操作できるプロトタイプで確認できたことは非常に効果的でした。現場のスタッフから具体的な意見を集めやすいだけでなく、リリース後に現場が受け入れやすくなるメリットもあったと思います」(深見氏)
導入はSTEP1とSTEP2の2段階に分けて進められた。STEP1ではものづくリンクを導入して生産準備プロセスのシステム化に取り組んだ。これには、生産手配管理、品目マスター、部品表、設計変更管理、ドキュメント管理、原価計算、ワークフロー、帳票などのドキュメントの自動生成といった機能が含まれ、車型情報や図面情報などを統合的に管理できるようになったという。
他のシステムとの連携も強化した。例えば、生産準備システムの情報は生産体制に移る段階で生産管理システムへと引き渡すことになる。以前は手入力で行っていたこの作業だが、ものづくリンクへの刷新によって自動でのデータ移行を実現している。他にも組織構成や人事情報などの各種マスターとの連携機能が組み込まれた。
STEP2では日程管理(進捗管理)に関する機能を追加した。以前は、車型担当者が決めた日程は限られたメンバーだけに共有されており、他のメンバーはその都度問い合わせる必要があった。現在は、さまざまな日程表をものづくリンクで共有し、他のメンバーでも参照できるようにしている。
「お客さまとのやり取りや車型情報から、ルールに基づいて日程を作成できるようにしました。作成した後にお客さまのご要望から調整が必要になることもありますが、今の時期にやるべきこと、この後の進行への影響などがすぐに判断ができます」(日下氏)
部品評価が終えれば原価計算が完了、日程の共有で今やるべきことも明確に
2020 年にSTEP1、2021年にSTEP2が稼働した。そしてものづくリンクで作った生産準備システムは「KIES」(KYOHO IntegratedEngineering System)という愛称で呼ばれ、親しまれている。
情報一元化の効果として、よく使われるのが日程や部品などの検索だった。「車型ごとの日程、生産台数、立ち上がりの時期、材質や調達先などもすべてKIESに蓄積されているので、検索すればすぐに欲しい情報が得られるようになりました。以前負担になっていた、情報を知っている人を探して確認することもなくなり、業務がスムーズに進むようになりました」(日下氏)
またいくつもの部署間で調整により膨大な時間を要していた原価計算も、部品評価すれば金額が算出されるようになり、大幅に短縮された。
これらの恩恵もものづくリンクが浸透し、データが蓄積されるようになったからといえる。
「KIESに情報が集約された結果、自然にみんなの目線が集まるようになってきました。意識の面でも変化が感じられます」(島谷氏)
STEP1、STEP2と進めてきたが、深見氏は「STEP3以降も視野に入れている」と述べ、今後取り組みたいテーマとして「見せる化」を挙げた。ここでいう見せる化とは、必要なタイミングでシステムから関係者に情報を提示していくこと。例えば、不具合を見つけたらその場で撮影をしてKIESに登録すると、上長や修正部門と即座に連絡を取り合い、即時に多角的な対応ができるようになる。深見氏は、「そのような見せる化をものづくりンクで実現していきたい」と期待を述べた。